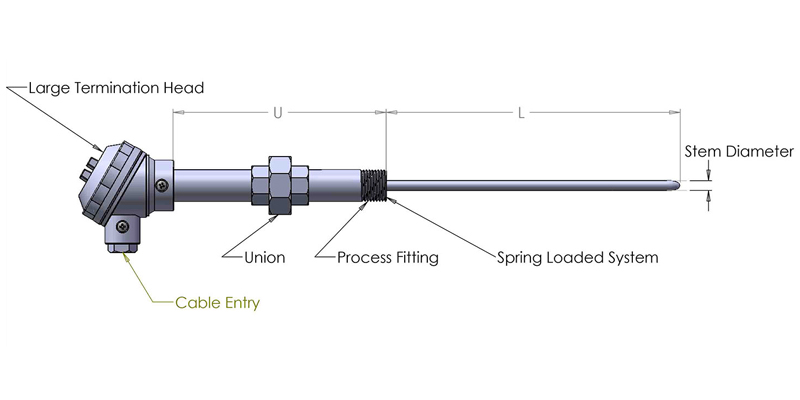
How do 2, 3 and 4 wire pt100 temperature sensors work?
To understand how 2, 3 and 4 wire pt100 temperature sensors work you must first understand what a temperature sensor is, what a PT100 is, and what the 2,3 and 4 wires are for.
What is a temperature sensor?
A Temperature sensor is a device that changes resistance at a predetermined rate in response to changes in temperature. They are circuit elements whose resistance increases with increasing temperature in a predictable manner.
What is a PT100?
A PT100 is the most common type of Resistance Temperature Detector (RTD). With a resistance of 100 Ohms at 0°C and 138.5 Ohms at 100°C. RTDs are categorised into industrial, as well as general purpose. You can find the datasheets in each product type here. Each type is available as a PT100, PT250, PT500 and PT1000.
A Pt100 features:
- A Platinum Resistant thermometer
- -200°C to 650°C temperature range
- ±0.1°C Accuracy
- 100Ω at 0°C Nominal resistance
PT100s are a common choice for measuring temperature in industrial processes and laboratories. They are a popular choice due to their stability, accuracy, and repeatability. They are frequently selected over thermocouples, due to the belief that they are more accurate. Whilst this is the case, it is usually not accuracy that a user is after, but repeatability. A user may see a slight variation in the temperature readout which may not be a critical issue. It is repeatability that is more critical so you can be assured to get the same result each time you take a temperature readout. The PT100 is a highly accurate temperature sensor. It is a well-suited sensor in a noisy environment, around generators, mechanical noise, motors, and high voltage.
Temperature Ranges
The internal assembly construction falls into low and high temperature ranges.
Low: -200 Degrees Celsius to +250 Degrees Celsius High: -200 Degrees Celsius to +600 Degrees Celsius Low temperature: 3mm, 4.8mm, 6mm, 8mm, 9.5mm diameter 316 stainless steel tube alumina powder filled. High Temperature: 3mm, 6mm diameter 316 stainless steel metal-sheathed mineral insulated.
What is the History of RTDs Resistance Temperature Detector?
In 1871 Werner von Siemens invented the Platinum Resistance Temperature Detector and presented a three-term interpolation formula. Siemens’ RTD rapidly fell out of favour due to the instability of the temperature reading. Hugh Longbourne Callendar developed the first commercially successful platinum RTD in 1885.
RTDs have become an industry standard. Historically RTDs were quite fragile, made of ceramic and fine wire. They did not handle vibration or shock well and were relatively expensive as compared to thermocouples. Applications need to be carefully analysed to ensure suitability. More recently RTDs are manufactured with a flat film element. These are inexpensive and less prone to the problems associated with the older style constructions. The flat film suffers from accuracy degradation as temperature goes up, however as most applications are below 250oC, this is not a major issue.
What is the pricing of RTDs Resistance Temperature Detector?
The price of RTDs typically was 20-30% higher than a thermocouple, plus when you moved into devices capable of measuring very high temperature, they would become quite expensive due to the materials required and construction techniques. With the innovations over the past 10 years, elements are less expensive and more robust.
For lower temperature measurement, with RTD prices are coming down, typically a PT100 has become the industry standard.
What is the design of RTDs Resistance Temperature Detector?
RTDs Resistance Temperature Detector (RTD). are designed to ensure precise and repeatable temperature versus resistance characteristics. The type of material used in RTD construction will determine the limits on the temperature to which the RTD can be exposed. The sensing element in an RTD is an electrical resistor that changes the resistance value as the temperature changes. The change in resistance with temperature happens at a predictable rate and can be measured to provide the temperature of a material of process.
The sensing element in an RTD typically contains either a coil of wire or a substrate with an etched film of platinum. The use of extension wires attached to the sending element allows the electrical resistance to be measured from a distance away from the process or material being measured. A protective sheath (normally stainless steel) houses the sensing element. Platinum is typically the material of choice in an RTD as this allows for a larger temperature range and it is a more stable material. Nickel and copper can also be used in RTD construction if a lower temperature range is required.
Table 1. Outline usable temperature ranges for each material.
The type of wire insulation used in an RTD also influences the temperature an RTD can be exposed to.
Table 2A. refers to the most used wire and insulation materials and their temperature limits. Table 2B. refers to the wires that connect the sensing element to the control instrument or readout and temperature limits. Typical choices for wire insulation include nickel, nickel alloys, tinned copper, silver-plated copper, or nickel-plated copper.
For RTD construction, there are two methods most used. The most common is to place the RTD element and attached wires into a metal tube with a closed end. The tube is packed with a vibration dampening and/or heat transfer material, alumina powder in most cases, and seal the open end with silicone, epoxy, or ceramic cement.
An alternate construction method is the use of a mineral insulated metal sheath (MIMS) cable. The RTD element is inserted into a drilled hole and attached to nickel or copper wires insulated by Magnesium Oxide (MgO). The end is also insulated with MgO and welded closed. The other end has extension wires attached prior to sealing.
Once the temperature range and application have been determined, Pyrosales will select the most suitable materials and method of construction of the RTD.
2, 3 or 4 wire configurations
2-wire construction is the least accurate. 2-wire RTDs tend to be used with short lead wires or where close accuracy is not required.
3-wire construction is the most popular choice for industrial applications, whilst 4-wire construction is used in laboratories where close accuracy is imperative.
There are many options to consider when choosing the correct RTD element for your requirements:
- Temperature rating
- Tolerance, accuracy, and interchangeability
- Time response
- Distance from control or measuring equipment.
Features and Benefits
Accuracy. A special process combines strain-free construction with full winding support for dependable, accurate readings in standard RTD elements, and in flat film elements where platinum is etched onto a substrate.
High signal-to-noise output. Increases the accuracy of data transmission and permits greater distances between the sensor and the measuring equipment.
Interchangeability. Strain-free construction and precision trimming allow elements from different lots to be substituted without recalibration.
Sensitivity. Self-heating is minimised, allowing precise measurement. The temperature coefficient (alpha) is carefully controlled at the industry standard while insulation resistance values exceed IEC-751 standards.
Standardisation. Elements are available to meet or exceed the requirements of various standardisation agencies. IEC-751 standard tolerance classes A and B respectively are very well suited for industrial applications. Tolerance classes up to 1/10th DIN can also be supplied where higher accuracy is demanded.
Physical and chemical stability over a wide temperature range. Pyrosales uses a highly controlled manufacturing process. Standard elements are built to resist mechanical vibration and shock, however, where there is high exposure to mechanical vibration, specially manufactured military specification thick film RTD elements can be supplied to suit the application.
Repeatability. All elements exceed IEC-751 repeatability values even after long exposure to temperatures within the operating range.
When to use RTDs?
- When accuracy and stability are a requirement of the customer’s specification.
- When accuracy must extend over a wide temperature range.
- When area, rather than point-sensing, improves control.
- When a high degree of standardization is desirable.
Advantages:
Linear over wide operating range
- Wide temperature operating range
- High temperature operating range
- Interchangeability over wide range
- Good stability at high temperature
Disadvantages:
Low sensitivity
- Higher cost than thermocouples
- No point sensing.
- Affected by shock and vibration.
- Requires three or four-wire operation.
Installation
The main consideration when installing an RTD element is that there is sufficient immersion to ensure that the RTD is not averaging the temperature of the process and equipment or structure outside the process. The RTD is not a point-measurement device like a thermocouple, so there is an active sensing area that needs to be fully immersed to ensure that the RTD is measuring the actual process temperature. A good thermal transfer along the shaft of the sensor for 40mm is critical when installing a thermowell.
Figure 1 shows the active sensing area of an RTD sensor. This area will vary depending on the length of the RTD element used in the construction. Sensors can be designed to give an average temperature indication.
Pyrosales engineers are available to consult on various stages of any project, from the development and planning of a new project to modifying or upgrading an existing facility. Our staff is here to provide you with assistance and recommendations to ensure the best outcome and value. We are happy to visit our clients on-site or conduct meetings at one of our offices.