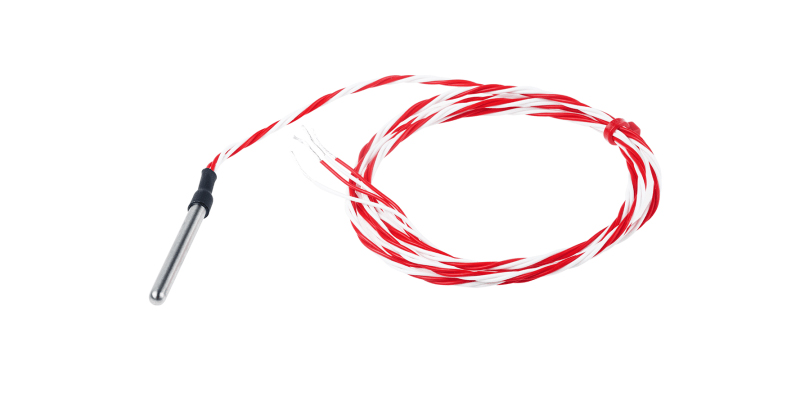
A Resistance Temperature Detector (RTD) is a temperature sensing device that consists of a wire coil or deposited film of pure metal. The element’s resistance increases with temperature in a known and repeatable manner, making them a reliable tool for measuring temperature within manufacturing applications. However, there are several factors that can affect the accuracy of RTDs:
- Temperature
- Wire length
- Wire Size
- Construction
Temperature
Because temperature affects the accuracy of RTD’s at different rates, there are standard RTD classifications. The most common classifications, as designated by the International Standard IEC 751, are Class A and Class B. Their accuracy is usually given as:
- Class A – ±0.06% of resistance or ±0.15°C at 0°C
- Class B – ±0.12% of resistance or ±0.30°C at 0°C
This tolerance is strictly at 0°C – it will change as temperature increases. This is calculated using the following equations where T is the temperature of the RTD in °C:
- Class A – ±(0.15+0.002T)°C
- Class B – ±(0.30+0.005T)°C
Wire Length and Wire Size
Wire length and size also need to be considered when calculating RTD sensor accuracy. The lead wire length can cause the tolerance to increase. The tolerances shown above are just for the RTD element itself. Adding wire to the element adds resistance to the circuit, which changes the reading of the sensor as a whole. Since low resistance wire is typically used with RTD construction, this added resistance will not affect the reading very much. However, when designing an application, it is important to know that as wire length increases or wire size decreases, the sensor will become less accurate.
Construction
When accuracy is an important part of the application, there are two ways to construct an RTD that will ensure more accurate readings:
- Use a 3-wire RTD
- Use a 1000 ohm RTD in lieu of a 100 ohm RTD
When using a 3-wire RTD, it is also necessary to use a temperature controller. The controller essentially cancels out the resistance coming from the lead wire attached to the RTD element. Assuming that all three wires are of equal length, the reading from the controller is of the RTD element itself.
For 1000 ohm RTD’s the change in resistance for each degree is much smaller than a 100 ohm RTD. The added resistance of the lead wire becomes negligible because it is a very small number when added to the 1000 ohm circuit.
It is important to consider all of these factors when designing an accurate RTD for your application. If you are unsure of the best RTD design for your application, contact Aavad Instrument Pvt. Ltd. for guidance. Aavad Instrument Pvt. Ltd. offers a complete line of Temperature Sensors to meet your needs.