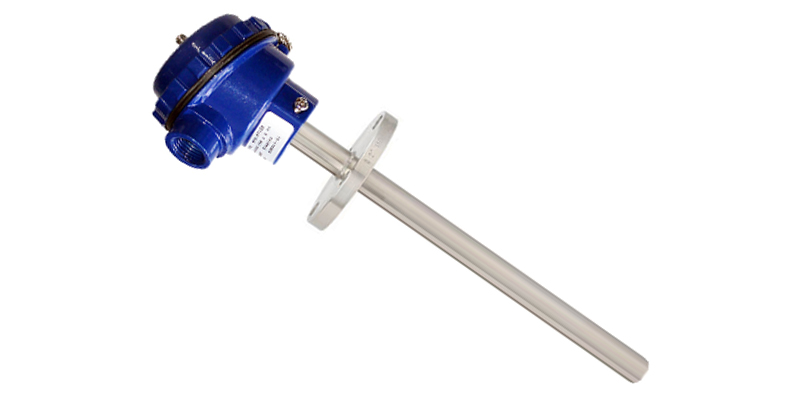
Introduction:
Metal tube measurement thermocouples are widely used in various industrial applications for precise temperature sensing and monitoring. These thermocouples consist of two dissimilar metal wires or elements that are joined together at one end to form a junction. The junction is inserted into a protective metal tube, which provides mechanical support and insulation. This blog post aims to provide a comprehensive understanding of metal tube measurement thermocouples, their working principles, applications, advantages, and limitations.
- Working Principle of Metal Tube Measurement Thermocouples: Metal tube measurement thermocouples operate on the principle of the Seebeck effect, which states that when two dissimilar metals are joined at a junction and exposed to a temperature gradient, a voltage is generated across the junction. This voltage is directly proportional to the temperature difference between the hot junction and the reference junction (usually kept at a known temperature).
- Construction and Design: Metal tube measurement thermocouples consist of several key components, including the thermocouple wires, junction, insulation, and protective metal tube. The choice of thermocouple wire material depends on the temperature range and the specific application requirements. Common thermocouple types include Type K (chromel/alumel), Type J (iron/constantan), and Type T (copper/constantan). The junction is typically created by welding or twisting the wires together. The metal tube provides protection against harsh environments, mechanical stresses, and electromagnetic interference.
- Advantages of Metal Tube Measurement Thermocouples: Metal tube measurement thermocouples offer several advantages, making them suitable for a wide range of applications:
- High durability and resistance to corrosion and oxidation.
- Excellent response time and accuracy in temperature measurements.
- Versatility in terms of temperature range and compatibility with various industrial processes.
- Immunity to electromagnetic interference.
- Flexibility in design and installation.
- Applications of Metal Tube Measurement Thermocouples: Metal tube measurement thermocouples find applications in numerous industries, including:
- Petrochemical and chemical processing plants
- Power generation facilities
- Food and beverage industry
- HVAC systems
- Automotive manufacturing
- Aerospace and aviation
- Research and development laboratories
- Limitations and Considerations: While metal tube measurement thermocouples offer many advantages, it is essential to consider their limitations and take appropriate precautions:
- Thermal response time may vary depending on the tube size and insulation material.
- The protective metal tube can introduce a thermal lag, especially in fast-changing temperature environments.
- Proper grounding and shielding are necessary to minimize electrical noise and electromagnetic interference.
- Selection of the correct thermocouple type based on the application requirements is crucial.
- Installation and Mounting Considerations: Proper installation and mounting of metal tube measurement thermocouples are crucial to ensure accurate and reliable temperature measurements. Some key considerations include:
- The junction placement: The location of the junction within the metal tube should be carefully determined based on the specific application requirements and the temperature gradient being measured.
- Thermal contact: Ensuring good thermal contact between the junction and the measured object is essential for accurate temperature sensing. Proper coupling methods, such as using thermal paste or compression fittings, should be employed.
- Protection against vibrations and mechanical stresses: Metal tube thermocouples should be adequately supported and protected against vibrations, mechanical shocks, and stress to prevent damage to the wires or the junction.
- Calibration and Accuracy: Calibration is an essential aspect of using metal tube measurement thermocouples to maintain accurate temperature readings. Due to the inherent measurement errors associated with thermocouples, periodic calibration against a known reference temperature is necessary. Calibration helps determine the thermocouple’s response characteristics and enables the application of compensation techniques to enhance measurement accuracy.
- Signal Conditioning and Readout: Metal tube measurement thermocouples generate a voltage signal that requires proper conditioning and conversion for accurate temperature measurement. Signal conditioning circuits, such as temperature transmitters or thermocouple amplifiers, are often used to amplify, linearize, and convert the thermocouple voltage into a standardized temperature output (e.g., 4-20 mA or 0-10 V). The processed signal can then be interfaced with control systems, data acquisition systems, or temperature controllers.
- Troubleshooting and Maintenance: Like any measurement device, metal tube measurement thermocouples may encounter issues or require periodic maintenance. Some common troubleshooting tips include:
- Checking for loose or damaged connections.
- Verifying proper grounding and shielding.
- Inspecting the metal tube for signs of corrosion or physical damage.
- Comparing temperature readings against a known reference source to identify calibration drift.
- Performing regular maintenance, such as cleaning and replacing damaged insulation or protective tubes.
- Emerging Trends and Future Developments: The field of temperature measurement is continually evolving, and metal tube measurement thermocouples are subject to ongoing advancements. Discuss some emerging trends and future developments, such as miniaturization of thermocouples, wireless temperature sensing, and advancements in signal processing and calibration techniques.
Conclusion:
Metal tube measurement thermocouples play a crucial role in temperature sensing and monitoring in various industrial applications. By considering installation factors, calibration procedures, signal conditioning, and maintenance requirements, users can maximize the accuracy and reliability of their temperature measurements. Staying informed about emerging trends ensures that engineers and technicians are aware of the latest developments in the field, allowing them to make informed decisions and optimize temperature control processes in their respective industries.