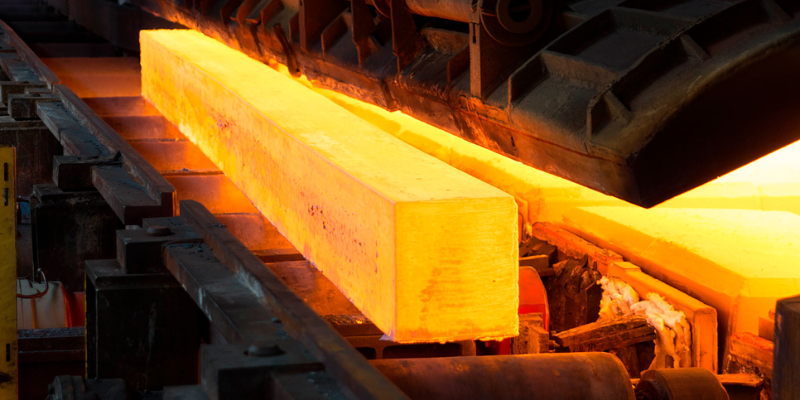
In the world of metalworking, rolling mills are essential for shaping and finishing metal products. Whether you’re producing sheets, plates, or other metal forms, controlling the temperature is critical for ensuring quality and efficiency. Here’s why temperature measurement is necessary in rolling mills:
1. Material Properties and Quality Control
Temperature directly influences the mechanical properties of the metal being processed. Metals exhibit different behaviors at various temperatures, including changes in:
- Strength and Hardness: At higher temperatures, metals typically become softer and more malleable, making them easier to shape. Conversely, lower temperatures can make metals harder and more brittle.
- Ductility: Elevated temperatures increase ductility, allowing the metal to stretch and bend without breaking.
- Grain Structure: Proper temperature control ensures a uniform and fine grain structure, which is crucial for the metal’s final properties.
Accurate temperature measurement helps maintain the desired properties, ensuring consistent quality in the final product.
2. Energy Efficiency
Rolling mills consume significant amounts of energy, particularly for heating the metal. Monitoring and controlling the temperature can lead to substantial energy savings by:
- Preventing Overheating: Avoiding unnecessary heating not only saves energy but also reduces wear and tear on the equipment.
- Optimizing Heat Use: Ensuring the metal is at the right temperature at each stage of the rolling process minimizes energy waste.
Efficient energy use also contributes to a more sustainable and cost-effective operation.
3. Process Optimization
The rolling process involves multiple stages, each requiring precise temperature control:
- Pre-heating: The metal is pre-heated to a specific temperature to make it easier to roll.
- Rolling Stages: Throughout the rolling process, temperature needs to be maintained within a specific range to ensure the metal flows correctly and achieves the desired dimensions.
- Cooling: After rolling, controlled cooling is necessary to achieve the desired metallurgical properties.
Accurate temperature measurement at each stage allows for real-time adjustments, optimizing the process and improving overall productivity.
4. Safety
Working with metals at high temperatures poses significant safety risks. Monitoring the temperature helps mitigate these risks by:
- Preventing Overheating: Reducing the risk of equipment failure or accidents caused by overheating.
- Ensuring Safe Handling: Ensuring metals are at safe temperatures for handling and further processing.
Maintaining safe temperature levels is crucial for protecting both workers and equipment.
5. Predictive Maintenance
Temperature measurement can be an integral part of predictive maintenance programs. By monitoring the temperature of both the metal and the equipment, potential issues can be identified before they lead to failures:
- Detecting Anomalies: Sudden changes in temperature can indicate equipment malfunctions or the need for maintenance.
- Extending Equipment Life: Maintaining optimal operating temperatures reduces wear and tear, prolonging the lifespan of the equipment.
This proactive approach helps avoid costly downtime and enhances the reliability of the rolling mill.
6. Real-Time Data Analysis and Control Systems
Modern rolling mills integrate sophisticated data analysis and control systems to monitor temperature in real-time. These systems offer several advantages:
- Instant Feedback: Real-time temperature data allows for immediate adjustments in the rolling process, minimizing deviations and ensuring consistent quality.
- Automation: Advanced control systems can automate temperature adjustments, reducing the need for manual intervention and improving precision.
- Data Logging: Continuous data logging helps in analyzing trends and optimizing the process over time.
Integrating these technologies can significantly enhance operational efficiency and product quality.
7. Thermocouples and Infrared Sensors
Different temperature measurement technologies are employed in rolling mills, each with its own advantages:
- Thermocouples: These are widely used for their accuracy and ability to measure high temperatures. They are durable and can be embedded in the rolling mill equipment to provide continuous temperature readings.
- Infrared Sensors: These non-contact sensors are ideal for measuring the temperature of moving metal surfaces. They offer quick response times and can measure temperature without physical contact, reducing wear and tear.
Choosing the right technology depends on the specific requirements of the rolling mill and the type of metal being processed.
8. Calibration and Maintenance
Ensuring the accuracy of temperature measurement devices is crucial for reliable data. Regular calibration and maintenance are essential:
- Calibration: Periodic calibration against standard references ensures that the measurement devices provide accurate readings. This is especially important in high-precision applications.
- Maintenance: Regular maintenance helps in detecting and addressing issues such as sensor drift or damage, which can affect measurement accuracy.
A robust calibration and maintenance program is necessary for sustaining the reliability of temperature measurement systems.
9. Temperature Gradients and Thermal Profiles
Understanding temperature gradients and thermal profiles within the metal during the rolling process is critical:
- Temperature Gradients: Temperature can vary significantly across the thickness of the metal. Monitoring these gradients helps in ensuring uniform properties throughout the product.
- Thermal Profiles: Creating a thermal profile of the rolling process, from pre-heating to cooling, helps in identifying critical points where temperature control is most crucial.
Analyzing these factors allows for a more detailed understanding of the process and aids in fine-tuning it for optimal results.
10. Impact on Microstructure and Mechanical Properties
The temperature during the rolling process has a profound impact on the microstructure of the metal, which in turn affects its mechanical properties:
- Phase Transformations: Certain metals undergo phase transformations at specific temperatures. Controlling temperature precisely ensures that these transformations occur as desired, leading to improved mechanical properties.
- Residual Stresses: Improper temperature control can lead to residual stresses in the metal, which can cause warping or failure in the final product. Monitoring and controlling temperature helps in minimizing these stresses.
By understanding and controlling these aspects, rolling mills can produce metal products with superior performance characteristics.
11. Integration with Other Sensors and Monitoring Systems
Temperature measurement is often integrated with other sensors and monitoring systems to provide a comprehensive view of the rolling process:
- Force and Pressure Sensors: These sensors measure the force and pressure applied during rolling, which, combined with temperature data, provides a complete picture of the process conditions.
- Speed Sensors: Monitoring the speed of the rolling mill and the movement of the metal helps in correlating temperature with other process parameters.
This integrated approach enables a more holistic understanding of the rolling process and aids in achieving better control and optimization.
Conclusion
Advanced temperature measurement techniques and technologies play a vital role in the modern rolling mill industry. They provide critical data that enhances quality control, energy efficiency, process optimization, safety, and predictive maintenance. By leveraging real-time data analysis, sophisticated control systems, and a comprehensive understanding of thermal profiles, rolling mills can achieve higher precision and efficiency, leading to superior metal products and more streamlined operations.