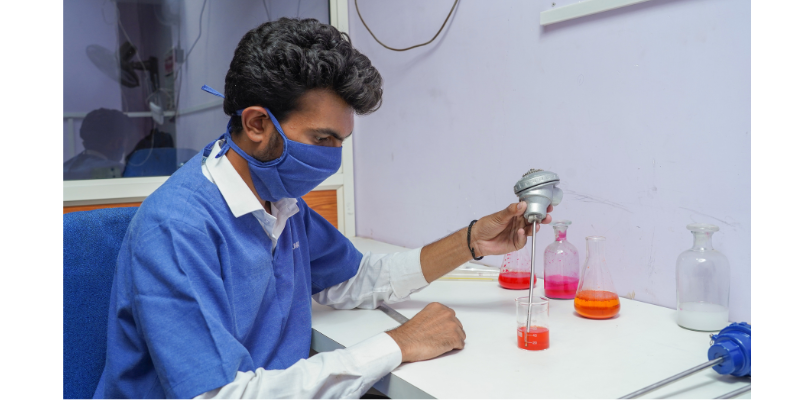
In the fast-paced and precision-driven world of industrial manufacturing, maintaining accuracy and reliability is paramount. Calibration plays a crucial role in ensuring that instruments used in various industrial applications deliver accurate results. Here’s why calibration is essential for industrial instruments, especially in sectors like temperature measurement in rolling mills:
1. Ensuring Accuracy
Calibration involves comparing the measurements of an instrument with a standard or known value. This process ensures that the instrument is providing accurate readings. In industries where precision is key, such as rolling mills, even a small deviation in temperature readings can lead to significant issues in the final product quality.
2. Maintaining Compliance
Many industries are governed by strict regulations and standards. Regular calibration ensures that instruments comply with these regulations, avoiding potential legal and financial penalties. For instance, ISO and other international standards often require regular calibration to maintain certification.
3. Enhancing Safety
In industrial environments, safety is of utmost importance. Instruments that measure critical parameters like temperature, pressure, and humidity need to be accurate to prevent hazardous conditions. Calibration helps in identifying and rectifying any discrepancies, thus enhancing workplace safety.
4. Optimizing Performance
Well-calibrated instruments ensure that the industrial processes run smoothly and efficiently. Accurate measurements lead to better control over processes, reducing wastage and improving productivity. In a rolling mill, precise temperature control is essential to produce high-quality steel products, and calibration helps achieve this.
5. Extending Equipment Lifespan
Regular calibration and maintenance of instruments can extend their lifespan. By detecting potential issues early, calibration helps in avoiding major breakdowns and costly repairs. This proactive approach ensures that the equipment operates reliably over a longer period.
6. Building Customer Trust
Delivering consistent and high-quality products builds trust with customers. When clients know that an industrial facility prioritizes precision through regular calibration, it enhances the company’s reputation and reliability in the market. This is particularly important in competitive industries where quality differentiates the leaders from the rest.
7. Cost Efficiency
Although calibration incurs a cost, it is a cost-saving measure in the long run. By ensuring instruments are working correctly, calibration reduces the likelihood of production errors, product recalls, and operational downtimes. Accurate instruments contribute to efficient resource usage and lower operational costs.
8. Supporting Technological Advancements
As industrial technologies evolve, the precision of instruments also increases. Calibration supports these advancements by ensuring that the latest, more sophisticated instruments are measuring accurately. This continuous process helps in keeping up with technological changes and integrating new instruments into existing systems without compromising accuracy.
9. Reducing Variability
In manufacturing, consistency is key. Calibration helps reduce variability in measurements, ensuring that each product or batch meets the same high standards. This consistency is crucial for maintaining brand integrity and customer satisfaction, especially in industries where product uniformity is vital.
10. Facilitating Traceability
Calibration records provide a traceable history of instrument performance. This traceability is important for audits, quality assurance processes, and identifying when an instrument may have started to deviate from its required accuracy. Having a documented calibration history can be critical in troubleshooting and optimizing production processes.
11. Enhancing Data Integrity
In the age of data-driven decision-making, the integrity of the data collected by industrial instruments is paramount. Calibration ensures that the data collected is accurate and reliable, forming a solid foundation for analysis, decision-making, and process improvements.
12. Supporting Research and Development
In R&D settings, the accuracy of instruments is essential for validating new processes and technologies. Calibration ensures that the data collected during research and development is precise, helping in the development of innovative solutions and improvements in industrial processes.
13. Meeting Customer Specifications
Many customers have specific requirements and tolerances for the products they receive. Calibration ensures that instruments used in the manufacturing process can meet these stringent customer specifications, leading to higher customer satisfaction and fewer returns or rework.
14. Improving Process Control
Accurate instruments are essential for maintaining tight process control. Calibration helps in achieving the desired control over various industrial processes, leading to better product quality and consistency. This is particularly important in critical applications where precise control can significantly impact the final product.
15. Minimizing Waste and Scrap
Accurate measurement and control reduce the amount of waste and scrap produced during manufacturing. By ensuring that instruments are correctly calibrated, manufacturers can minimize errors that lead to defective products, thus saving materials and reducing environmental impact.
16. Boosting Competitive Advantage
Companies that invest in regular calibration demonstrate a commitment to quality and reliability. This dedication can be a significant competitive advantage, attracting more customers and potentially leading to increased market share.
Conclusion
Regular calibration of industrial instruments is a critical practice that offers numerous benefits beyond just compliance with regulations. It enhances accuracy, safety, and efficiency, while also supporting technological advancements and reducing operational costs. By ensuring that instruments provide precise measurements, calibration helps maintain high product quality, build customer trust, and achieve operational excellence. For industries like rolling mills, where precision in temperature measurement is crucial, regular calibration is an indispensable aspect of maintaining a competitive edge and ensuring long-term success.