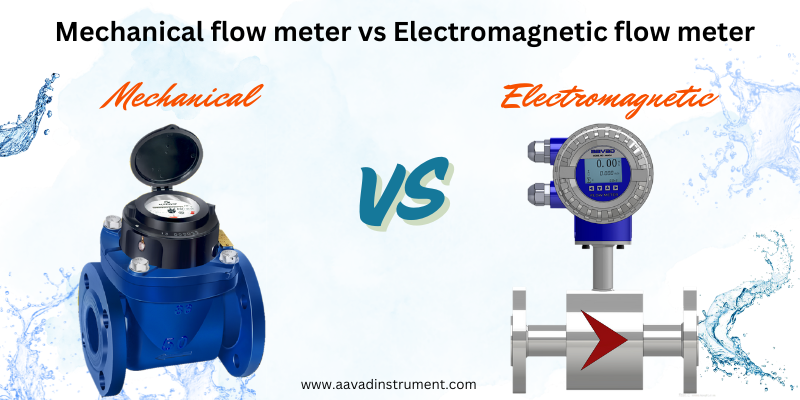
Mechanical Flow Meters vs Electromagnetic Flow Meters
Introduction
Flow meters are critical tools for monitoring and controlling fluid flow in various industries, from water treatment plants to oil and gas facilities. Choosing the right type of flow meter ensures optimal system performance, accuracy, and cost-effectiveness.
In this article, we will delve into the key differences, advantages, limitations, and applications of mechanical flow meters and electromagnetic flow meters to help you make an informed decision.
Understanding the Basics
What Are Mechanical Flow Meters?
Mechanical flow meters measure fluid flow using moving parts such as gears, turbines, or paddles. The fluid’s kinetic energy drives these components, and the resulting movement is translated into flow rate measurements.
Features of Mechanical Flow Meters:
- Direct measurement using mechanical movement.
- Wide range of models to suit different fluids and flow rates.
What Are Electromagnetic Flow Meters?
Electromagnetic flow meters, often called mag meters, rely on Faraday’s law of electromagnetic induction. They measure the velocity of conductive fluids by generating a magnetic field and detecting the voltage induced as the fluid flows through.
Features of Electromagnetic Flow Meters:
- Contactless measurement with no moving parts.
- Best suited for conductive liquids and slurries.
Advantages and Limitations: A Detailed Comparison
Advantages of Mechanical Flow Meters
- Low Initial Cost: Budget-friendly, making them accessible for small-scale applications.
- Versatile Fluid Compatibility: Can measure non-conductive fluids like oil, gas, and fuel.
- Simple Construction: Easy to install and operate in low-tech environments.
- No Power Supply Required: Operates purely on fluid dynamics.
Limitations of Mechanical Flow Meters
- Prone to Wear and Tear: Moving parts are susceptible to damage and require frequent maintenance.
- Inaccuracy with Contaminants: Solids, debris, or varying viscosities can affect performance.
- Pressure Drop: The presence of internal components causes resistance to fluid flow.
Advantages of Electromagnetic Flow Meters
- High Accuracy: Excellent for precise measurement in critical applications.
- No Moving Parts: Minimizes wear and reduces maintenance.
- Handles Slurries and Corrosive Liquids: Ideal for industries like mining and chemical processing.
- No Pressure Loss: Allows smooth fluid flow without any obstruction.
- Large Size Range: Available for pipelines from small to very large diameters.
Limitations of Electromagnetic Flow Meters
- Restricted to Conductive Fluids: Cannot measure gases, oils, or non-conductive fluids.
- Higher Initial Investment: Costs more upfront but may offer better lifecycle savings.
- Requires Power: Needs an external power source for operation.
Comparison Table: Key Differences
Feature | Mechanical Flow Meters | Electromagnetic Flow Meters |
---|---|---|
Operating Principle | Mechanical movement of internal parts. | Induced voltage in a magnetic field. |
Fluid Compatibility | All fluid types, including non-conductive. | Only conductive liquids. |
Maintenance Needs | Frequent due to wear and tear. | Minimal, no moving parts. |
Accuracy | Moderate, affected by fluid conditions. | High, unaffected by viscosity or density. |
Cost | Lower initial cost. | Higher initial cost. |
Pressure Drop | Yes, due to mechanical resistance. | No pressure drop. |
Power Supply | Not required. | Requires power supply. |
Applications in Different Industries
Mechanical Flow Meters: Where They Shine
- Oil and Gas: Suitable for measuring fuel and non-corrosive liquids.
- Industrial Processes: Low-budget operations needing moderate accuracy.
- Agriculture: Measuring water usage in irrigation systems.
Electromagnetic Flow Meters: Where They Excel
- Water and Wastewater Management: Accurate flow measurement for treatment plants.
- Mining and Slurry Handling: Handles abrasive slurries with ease.
- Food and Beverage: Ideal for hygienic processes and CIP (Clean-in-Place) systems.
- Chemical Processing: Handles corrosive liquids and precise dosing applications.
Selection Criteria: Choosing the Right Flow Meter
When deciding between a mechanical flow meter and an electromagnetic flow meter, consider the following factors:
- Type of Fluid: If the fluid is non-conductive (oil, gas, etc.), a mechanical flow meter is the only option. For conductive liquids, electromagnetic flow meters provide superior performance.
- Accuracy Requirements: Electromagnetic flow meters are better suited for critical applications where high accuracy is essential.
- Operating Environment: Harsh environments with corrosive or abrasive fluids demand the durability of electromagnetic meters.
- Budget: For cost-sensitive applications, mechanical flow meters may be more appropriate despite higher maintenance costs.
Why Choose AAVAD?
At SensoTemp, we specialize in delivering high-quality flow measurement solutions tailored to your needs. Our electromagnetic flow meters are designed for precision, durability, and minimal maintenance, making them the perfect choice for water, wastewater, and industrial applications.
- Certified Quality: NABL calibration ensures accuracy and compliance.
- Expert Support: Our team provides guidance on installation and usage.
- Affordable Pricing: Competitive rates with long-term value.
Conclusion
Choosing the right flow meter depends on your application, fluid type, and budget. While mechanical flow meters remain a cost-effective solution for basic needs, electromagnetic flow meters offer superior accuracy, durability, and functionality for modern industries.
Contact AAVAD today for expert advice and explore our range of flow measurement solutions!