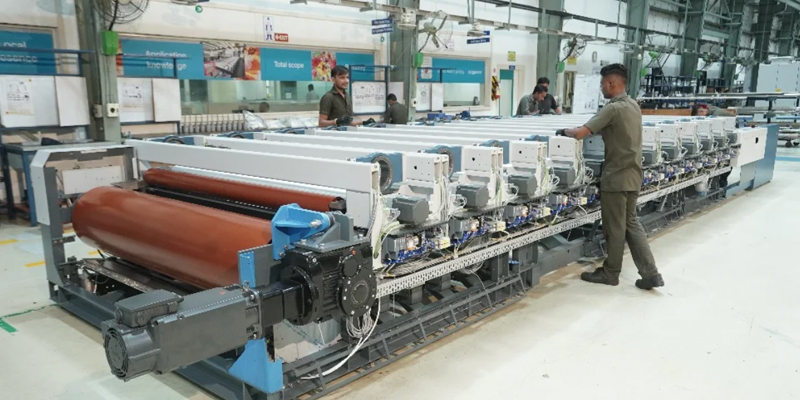
RTD Sensors in Rotary Print Machines
Rotary print machines are widely used in the textile industry for high-speed, precise, and continuous fabric printing. Maintaining optimal temperature conditions in these machines is crucial for achieving consistent print quality, preventing defects, and ensuring efficient operation. Resistance Temperature Detectors (RTD) sensors, particularly Pt100 sensors, play a vital role in temperature measurement and control in rotary print machines.
Why Temperature Control Matters in Rotary Printing
Rotary printing involves transferring dye or pigment onto fabric using engraved rotary screens. The process requires controlled heating for drying, curing, and color fixation. Any temperature fluctuations can lead to:
- Uneven prints – Temperature inconsistencies may cause color variations or smudging.
- Defective output – Excessive heat can lead to fabric shrinkage, while insufficient heat can result in improper curing.
- Machine wear and tear – Overheating can damage machine components, leading to increased maintenance costs.
- Increased energy consumption – Poor temperature regulation can lead to higher power usage, raising operational costs.
- Ink consistency issues – Temperature variations can affect ink viscosity, leading to print defects.
Role of RTD Sensors in Rotary Print Machines
RTD sensors, specifically Pt100 sensors, are widely preferred in rotary print machines due to their high accuracy, stability, and repeatability. They are used to monitor and regulate temperature in various sections of the machine, including:
- Drying Units – The fabric passes through drying chambers where controlled heat is applied. RTD sensors ensure consistent temperature to prevent uneven drying.
- Heated Rollers – These rollers help in curing and fixing the dyes onto the fabric. RTD sensors provide real-time temperature feedback to avoid overheating.
- Steam Chambers – Many rotary print machines use steam for color fixation. RTD sensors help maintain the ideal steam temperature for uniform color penetration.
- Ink Reservoirs – Certain printing methods require precise ink temperature control to maintain viscosity and flow consistency.
- Heating Elements in Print Heads – Some advanced rotary print machines use heated print heads to ensure optimal ink application. RTD sensors help regulate their temperature.
- Environmental Monitoring – RTD sensors can be integrated to monitor ambient temperature, preventing unexpected fluctuations that affect the printing process.
Advantages of Using RTD Sensors in Rotary Print Machines
- High Accuracy: Pt100 RTDs offer precise temperature readings, ensuring optimal process control.
- Durability: Designed to withstand high temperatures and harsh industrial environments.
- Long-Term Stability: RTD sensors have minimal drift over time, reducing recalibration frequency.
- Compatibility with Automation Systems: Easily integrated with PLCs and temperature controllers for automated process control.
- Energy Efficiency: Proper temperature regulation reduces power consumption, leading to cost savings.
- Reduction in Machine Downtime: Consistent monitoring prevents overheating issues that can cause machine breakdowns.
Choosing the Right RTD Sensor for Rotary Printing Applications
When selecting an RTD sensor for a rotary print machine, consider factors like:
- Temperature Range: Ensure the sensor can operate within the required temperature limits.
- Probe Material: Stainless steel or ceramic probes are ideal for high-temperature environments.
- Response Time: Faster response times improve temperature regulation and process efficiency.
- Mounting Options: Sensors should be positioned for optimal thermal contact with the measured surface.
- Accuracy Class: Higher accuracy RTDs (Class A or 1/10 DIN) provide better performance in critical applications.
Best Practices for RTD Sensor Maintenance
To ensure long-term performance, follow these maintenance tips:
- Regular Calibration: Periodic calibration maintains accuracy and prevents drift.
- Proper Installation: Secure mounting ensures accurate readings.
- Protection from Contaminants: Shield sensors from dust, moisture, and chemical exposure.
- Monitor Wiring and Connections: Loose or damaged connections can affect sensor performance.
Conclusion
RTD sensors, especially Pt100 models, are essential for maintaining precise temperature control in rotary print machines. Their accuracy, stability, and durability contribute to improved print quality, reduced waste, and enhanced efficiency. Investing in high-quality RTD sensors ensures a seamless textile printing process, minimizing defects and maximizing productivity.
For high-performance RTD sensors suitable for rotary print machines, AAVAD offers reliable solutions tailored to industrial applications. Contact us today to learn more!