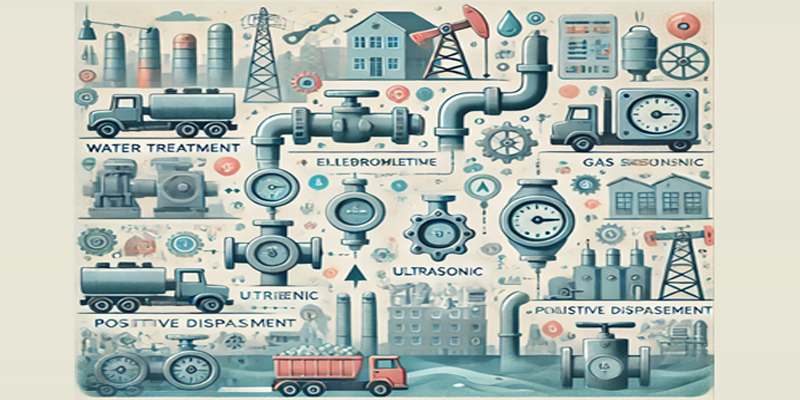
How to select the Perfect Flow Meter for Any Application:
How can you choose the ideal flow meter for your application in the realm of industrial processes? We frequently undervalue the significance of precise flow measurement, despite the fact that it affects everything from operational effectiveness to product quality. Because of this, choosing a flow meter is a crucial choice that needs thorough evaluation.
We’ll go over the important considerations to make when choosing a flow meter for your particular need. We will go over everything, from comprehending the fundamentals of flow measurement to examining your fluid and process. In order to help you make an informed decision, we will also examine other flow meter alternatives. You will be able to choose the ideal flow meter for any application by the end.
1. Understand the Fluid Type
- The choice of a flow meter depends significantly on the type of fluid you need to measure. Common fluids include water, oil, chemicals, gases, and steam.
- Characteristics to consider:
- Viscosity: Thick, sticky fluids like oil need specific types of meters like positive displacement or Coriolis.
- Conductivity: Fluids with high conductivity work well with electromagnetic flow meters, while non-conductive fluids may require ultrasonic or turbine meters.
- Cleanliness: Dirty or particle-laden fluids can clog sensitive meters like turbines. For such cases, electromagnetic or ultrasonic flow meters might be more suitable.
2. Define the Flow Range and Accuracy Needs
- Flow Range: Choose a flow meter that can operate efficiently within the minimum and maximum flow rates required by your application.
- Accuracy Requirements: Applications requiring high accuracy, such as chemical dosing, might benefit from Coriolis or thermal mass flow meters. Applications like wastewater management, where precision is less critical, may perform well with simpler, less precise meters.
3. Consider Installation Requirements
- Pipe Size and Orientation: Some flow meters, such as ultrasonic or electromagnetic types, are ideal for larger pipe diameters. Inline models need a consistent pipe diameter for accurate readings.
- Location Constraints: Limited space may affect your choice. Some meters, like clamp-on ultrasonic models, are easier to install in tight spaces.
- Straight Pipe Lengths: Turbulence can affect accuracy, so some meters require a certain length of straight pipe upstream and downstream to minimize flow disturbances.
4. Evaluate Pressure and Temperature Conditions
- Certain flow meters, such as thermal mass flow meters, are sensitive to temperature variations. Check that the chosen meter can withstand your process’s operating temperature and pressure range.
- High-pressure applications might necessitate robust models like turbine or Coriolis meters, which can handle pressure fluctuations without compromising accuracy.
5. Choose the Right Meter Type
- Electromagnetic Flow Meters: Ideal for conductive fluids, offering high accuracy and low pressure drop. They are commonly used in water and wastewater applications.
- Coriolis Flow Meters: Highly accurate, suitable for viscous and corrosive fluids. They work well in applications where precision is crucial, such as chemical and food processing.
- Ultrasonic Flow Meters: Good for both conductive and non-conductive fluids and suitable for large pipes. They are often used in situations requiring non-invasive installation.
- Turbine Flow Meters: Best for clean, low-viscosity fluids like water and fuel. They offer good accuracy but are susceptible to damage from particulate matter.
- Thermal Mass Flow Meters: Primarily used for gas measurement, offering excellent precision and sensitivity to low flow rates.
6. Assess Long-Term Maintenance and Lifecycle Costs
- Consider maintenance needs and operational costs over time. For instance, electromagnetic meters have no moving parts, reducing maintenance. Turbine meters, however, may require regular cleaning in certain applications.
7. Check Compatibility with System Outputs
- Choose a meter that can communicate with your control system. Some applications require real-time monitoring, which might necessitate meters with digital outputs or telemetry capabilities.
8. Environmental Factors
- For installations in harsh environments (like outdoor or hazardous areas), ensure the flow meter is rated for the environmental conditions. Weatherproof or explosion-proof enclosures are essential in certain industries, such as oil and gas.
Conclusion
Selecting the right flow meter involves analyzing your fluid type, flow requirements, installation setup, and environmental conditions. Careful consideration of these factors can ensure optimal performance and longevity of the flow meter in your application.