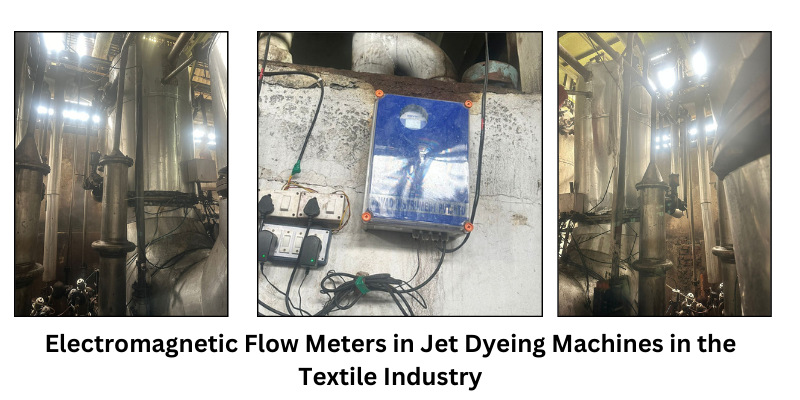
Jet dyeing machines are widely used in the textile industry for dyeing fabrics efficiently. Accurate measurement and control of the dyeing process are critical to ensuring high-quality output and optimal resource utilization. Electromagnetic flow meters are an excellent choice for measuring the flow of liquids in these machines due to their precision and reliability. This blog will discuss the working principles, benefits, and installation considerations of electromagnetic flow meters in jet dyeing machines.
Working Principles of Electromagnetic Flow Meters
Electromagnetic flow meters, or mag meters, operate based on Faraday’s law of electromagnetic induction. This principle states that a voltage is induced when a conductive fluid flows through a magnetic field. The key components of a mag meter include:
- Flow Tube: Contains the fluid and houses the electrodes and magnetic coils.
- Electrodes: Positioned inside the flow tube to measure the induced voltage.
- Magnetic Coils: Generate a magnetic field across the flow tube.
- Transmitter: Converts the induced voltage into a flow rate reading.
When the conductive dye solution flows through the magnetic field, a voltage proportional to the flow velocity is induced across the electrodes. The transmitter then processes this voltage to provide an accurate flow rate measurement.
Benefits of Electromagnetic Flow Meters in Jet Dyeing
- High Accuracy: Electromagnetic flow meters offer high accuracy, typically within ±0.5% of the actual flow rate, ensuring precise control over the dyeing process.
- No Moving Parts: The absence of moving parts minimizes maintenance and reduces the risk of mechanical failure, which is crucial in continuous dyeing operations.
- Wide Range of Applications: They are suitable for a wide range of conductive fluids, including dye solutions, making them versatile for different dyeing processes.
- Minimal Pressure Drop: The design of mag meters results in minimal pressure loss, maintaining the efficiency of the jet dyeing machine.
Installation Considerations
Proper installation of electromagnetic flow meters is essential to ensure accurate measurements and reliable operation. Here are some key considerations:
- Straight Pipe Length: Ensure sufficient straight pipe lengths before and after the meter to avoid flow disturbances. A typical recommendation is 5 to 10 times the pipe diameter upstream and 2 to 5 times downstream.
- Grounding: Proper grounding of the flow meter is crucial to eliminate electrical noise and ensure accurate readings. Follow the manufacturer’s guidelines for grounding procedures.
- Pipe Material Compatibility: The flow tube material should be compatible with the dye solution to prevent corrosion and ensure longevity. Common materials include stainless steel, PTFE, and other non-corrosive materials.
- Orientation: Install the flow meter in a location that remains filled with liquid at all times to avoid air pockets, which can affect accuracy. Horizontal installation is preferred, but vertical installation is possible if flow direction is upward.
- Environmental Factors: Consider the ambient temperature, humidity, and exposure to chemicals. Ensure the flow meter’s housing and electronics are rated for the specific environmental conditions of the installation site.
Case Study: Successful Implementation in a Textile Plant
To illustrate the benefits of electromagnetic flow meters, let’s consider a case study of a textile plant that integrated these meters into their jet dyeing machines.
Background: A textile plant faced issues with inconsistent dye quality and high operational costs due to inaccurate flow measurements using traditional flow meters.
Solution: The plant decided to install electromagnetic flow meters across all their jet dyeing machines. They chose meters with advanced features like bidirectional measurement, batch control, and temperature compensation.
Results:
- Improved Accuracy: The high accuracy of the mag meters ensured consistent dye quality across different batches.
- Reduced Maintenance: The lack of moving parts reduced maintenance requirements and downtime.
- Cost Savings: Precise control over dye solution usage led to significant cost savings in dye and water consumption.
- Enhanced Data Analysis: Integration with the plant’s data logging system provided valuable insights for process optimization.
Electromagnetic flow meters are an ideal solution for measuring and controlling the flow of dye solutions in jet dyeing machines in the textile industry. Their accuracy, reliability, and minimal maintenance requirements make them a preferred choice for textile manufacturers aiming to optimize their dyeing processes. By following proper installation guidelines, you can ensure the efficient operation of your jet dyeing machines and maintain high-quality dyeing standards.