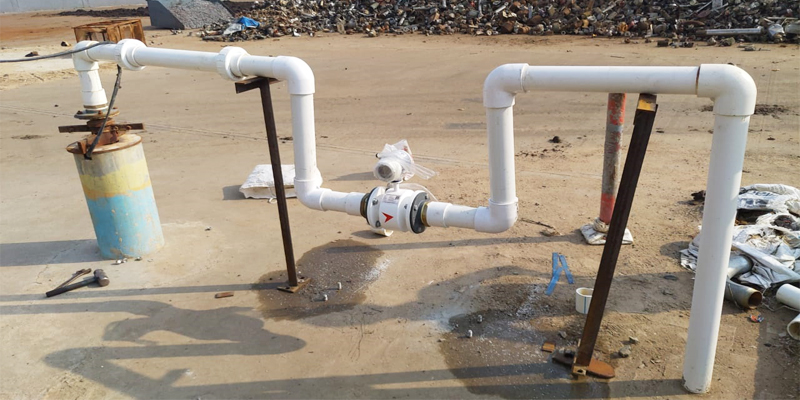
The electromagnetic flowmeter is used to measure the flow of conductive liquids and slurries a low as 5 Micro Siemens (including corrosive and abrasive) in closed pipes.
Magnetic Flow Meters
The performance of the instrument is not affected by the properties of the material such as corrosiveness, viscosity, pressure, density, acidity, and alkalinity.
It can measure the flow of liquids, pastes, and slurries in water, wastewater, chemical, fertilizer, dairy, food, beverage, pharmaceutical, medical, petrochemical, iron, steel, paper, mining, and agricultural industries, etc.
They are used to measure water flow cooling in steel and power plants. They have the ability to measure the flow of clean water, effluent, sludges, etc., in pollution and environmental control.
Installation Guidelines
The Primary Flow Tube can be installed at any point in the pipe run either horizontal or vertical provided the following conditions are met:
The direction of flow through the pipe is same as indicated on the primary flow tube by a red arrow.
Straight lengths of maximum 10 D on upstream and minimum 10 D on downstream as shown. If disturbances like corkscrewing or vortex flow conditions are present straight lengths should be increased or flow straighteners should be used. Flaps, slide gates, valves, etc should be arranged at a distance of at least 5D downstream of primary flow tube.
Ensure that primary flow tube remains completely filled by the fluid under measurement even under no-flow
condition. This ensures trouble-free and reliable operation of the Flow Meter. Select a location on the pipe,
which will always run full of liquid. For vertical installations, the direction of flow against Gravity ensures full pipe. Some of the recommended installations are as under :
Flange connections must be assembled concentrically on both the upstream and the downstream side. Measuring accuracy will be affected by turbulence in the liquid from poorly made connections.
Important: Gaskets and grounding rings must also be mounted concentrically!
The flow sensor should always be filled with liquid. For that reason, the flow sensor must not be mounted at the highest point of the pipe system or in free outlets, where gravity could empty or partially empty the pipe.
The flow sensor can be mounted vertically or horizontally. If the flow sensor is mounted vertically, the flow direction should always be upwards.
In that way, the effect of possible bubbles in the liquid will be significantly reduced, just as it will ensure that the flow sensor is always filled with liquid. In case the liquid is carrying particles, for example when measuring sludge, sewage, etc., the flow sensor must be mounted vertically.
When mounting horizontally in pipes with the free downstream outlets, the flow sensor should be mounted such that it will always be filled with liquid, for example in a bend situated lower than the height of the outlet.
In case the liquid is carrying particles, e.g. when measuring sludge, sewage, etc. the flow sensor must be mounted vertically.