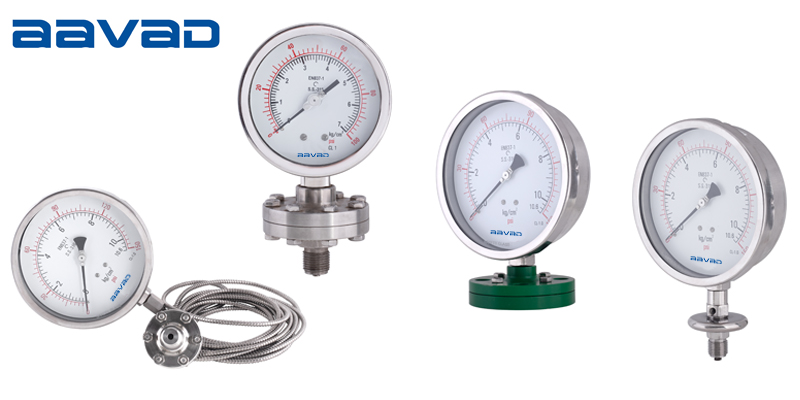
In industrial applications, accurate pressure measurement is crucial for ensuring safe and efficient operations. Heavy-duty industrial pressure gauges play a vital role in monitoring and controlling pressure in various industries, including manufacturing, oil and gas, chemical processing, and more. In this blog post, we will explore the key features, applications, maintenance tips, and selection considerations for heavy-duty industrial pressure gauges.
Understanding Heavy Duty Industrial Pressure Gauges:
- Definition and purpose of heavy-duty industrial pressure gauges.
- Types of pressure gauges: Bourdon tube, diaphragm, capsule, and more.
- Pressure range, accuracy, and measurement units.
Applications of Heavy Duty Industrial Pressure Gauges:
- Oil and gas industry: Wellhead monitoring, pipeline pressure control.
- Manufacturing industry: Hydraulic systems, pneumatic systems, compressor monitoring.
- Chemical processing: Reactor vessels, distillation columns, pressure vessels.
- Power generation: Boiler systems, turbine monitoring.
Key Features and Components:
- Sturdy construction: Materials, such as stainless steel, brass, or exotic alloys.
- Pressure sensing elements: Bourdon tube, diaphragm, or bellows.
- Dial face: Clear and easy-to-read scale, markings, and units.
- Pressure connection: Threaded, flanged, or welded options.
- Protection and safety features: Overpressure protection, blowout back, and hermetic sealing.
Maintenance and Calibration:
- Regular inspection and cleaning procedures.
- Calibration methods and intervals.
- Troubleshooting common issues.
- Replacing damaged parts or worn-out gauges.
Selecting the Right Pressure Gauge:
- Consideration factors: Pressure range, media compatibility, environmental conditions.
- Gauge size and mounting options.
- Accuracy requirements and certification standards.
- Cost-effectiveness and long-term durability.
Industry Regulations and Standards:
- Familiarization with relevant safety regulations and standards.
- Compliance with industry-specific requirements (ASME, API, ISO).
Common Challenges and Troubleshooting Tips:
- Gauge failure causes and troubleshooting techniques.
- Dealing with vibrations, pulsations, and extreme temperatures.
- Ensuring accurate readings and preventing gauge damage.
Future Trends in Industrial Pressure Gauges:
- Digital pressure gauge advancements.
- Wireless monitoring and IIoT integration.
- Predictive maintenance and condition monitoring.
Installation Considerations:
- Proper mounting and positioning of the pressure gauge.
- Ensuring a secure and leak-free connection.
- Taking into account vibration isolation and dampening measures.
- Considering the accessibility for maintenance and readability.
Specialized Pressure Gauges:
- High-pressure gauges: Designed to handle extremely high pressure levels.
- Low-pressure gauges: Sensitive instruments for measuring low-pressure systems.
- Differential pressure gauges: Used to measure the difference in pressure between two points.
- Vacuum gauges: Specifically designed for measuring pressure below atmospheric pressure.
Remote Monitoring and Data Logging:
- Integration with industrial control systems and SCADA (Supervisory Control and Data Acquisition) systems.
- Remote monitoring of pressure readings for real-time data analysis and decision-making.
- Data logging capabilities for historical analysis, troubleshooting, and performance optimization.
Hazardous Environments and Ex Safety:
- Pressure gauges with explosion-proof (Ex) certifications for use in hazardous areas.
- Understanding ATEX, IECEx, and other relevant certifications for intrinsically safe pressure gauges.
- Design considerations for withstanding corrosive, flammable, or volatile environments.
Calibration and Traceability:
- Importance of regular calibration to maintain accuracy.
- Calibration standards and procedures, including NIST (National Institute of Standards and Technology) traceability.
- Third-party calibration services and equipment verification.
Gauge Accessories and Instrumentation:
- Gauge isolators and snubbers for protection against pressure spikes and pulsations.
- Needle valves for fine control and isolation during calibration or maintenance.
- Gauge adapters and fittings for compatibility with different connection types.
- Gauge guards and protective covers for added durability and safety.
Training and Safety Practices:
- Proper training for personnel on the correct usage, handling, and maintenance of pressure gauges.
- Safety precautions when working with high-pressure systems and hazardous substances.
- Periodic safety audits to ensure compliance with safety protocols.
Remember to format your blog post appropriately with headings, subheadings, and bullet points to enhance readability. Including relevant images, diagrams, or real-life application examples can also make your blog more engaging and informative.
Heavy-duty industrial pressure gauges are essential tools for maintaining operational efficiency and safety in various industries. By understanding their features, applications, maintenance requirements, and selection considerations, industry professionals can make informed decisions to ensure accurate pressure measurement and optimize their processes. Stay updated with the latest advancements in pressure gauge technology to unlock new possibilities for your industrial operations.