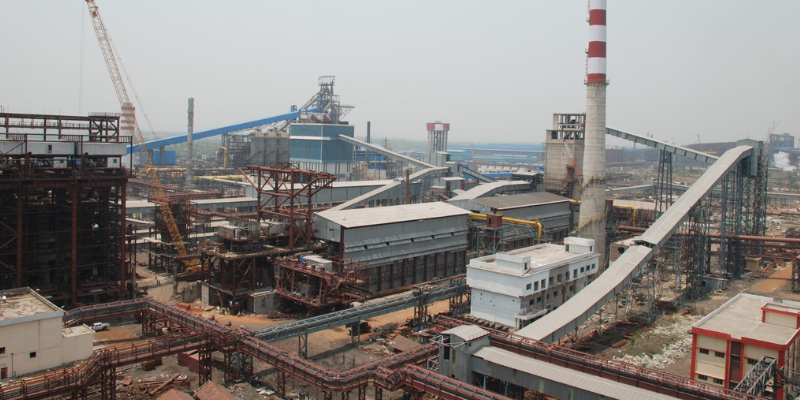
Thermocouples in Chhattisgarh Steel Plants
Thermocouples are crucial in steel plants for precise temperature measurement and control. In Chhattisgarh, a prominent hub for steel production, these devices play a vital role in ensuring optimal performance and quality.
Importance of Thermocouples in Steel Plants
- Accurate Temperature Measurement:
- Thermocouples provide accurate and reliable temperature readings, essential for various stages of steel production, including melting, casting, and rolling.
- Precise temperature control helps in maintaining the desired metallurgical properties of the steel.
- Process Control:
- Temperature monitoring through thermocouples allows for real-time process adjustments.
- Ensures consistent product quality and minimizes defects.
- Safety:
- High-temperature operations pose safety risks. Thermocouples help in maintaining safe operating conditions by monitoring and controlling extreme temperatures.
Types of Thermocouples Used
- Type K (Nickel-Chromium/Nickel-Alumel):
- Widely used due to its wide temperature range (-200°C to +1260°C).
- Suitable for general-purpose applications in steel plants.
- Type S (Platinum-Rhodium/Platinum):
- Used for high-temperature measurements (up to 1600°C).
- Offers high accuracy and stability, ideal for critical processes like smelting.
- Type B (Platinum-Rhodium):
- Suitable for extremely high temperatures (up to 1700°C).
- Often used in furnaces and kilns.
Applications in Chhattisgarh Steel Plants
- Blast Furnaces:
- Thermocouples monitor the temperature inside the furnace to ensure efficient smelting of iron ore.
- Help in optimizing fuel consumption and reducing emissions.
- Continuous Casting:
- Temperature measurement is critical in the continuous casting process to produce high-quality steel slabs.
- Ensures uniform cooling and solidification.
- Rolling Mills:
- In rolling mills, thermocouples are used to monitor and control the temperature of steel as it is shaped.
- Essential for achieving the desired mechanical properties and surface finish.
- Heat Treatment:
- Thermocouples ensure precise temperature control during heat treatment processes like annealing and tempering.
- Critical for enhancing the strength and durability of steel products.
Challenges and Innovations
- Harsh Environment:
- Steel plants present challenging conditions for thermocouples, including high temperatures, corrosive environments, and mechanical wear.
- Innovations in thermocouple materials and protective sheaths are addressing these challenges.
- Integration with Automation Systems:
- Modern steel plants in Chhattisgarh are increasingly integrating thermocouples with automated control systems.
- Enhances process efficiency, reduces human intervention, and improves safety.
- Data Analytics:
- Leveraging data from thermocouples for predictive maintenance and process optimization.
- Advanced analytics help in identifying potential issues before they lead to downtime or defects.
Enhanced Thermocouple Designs
- Mineral-Insulated (MI) Thermocouples:
- Feature a metal sheath and compacted mineral insulation, providing durability in high-pressure and high-temperature environments.
- Widely used in critical areas of steel plants where reliability and longevity are paramount.
- Sheathed Thermocouples:
- Equipped with protective sheaths made of materials like stainless steel, Inconel, or ceramic.
- Sheaths protect the thermocouple from corrosive and abrasive environments, extending the sensor’s lifespan.
- Dual Thermocouples:
- Combine two thermocouples within a single sheath, allowing for redundancy and improved reliability.
- Useful in critical processes where continuous temperature monitoring is essential, and downtime must be minimized.
Integration with Industry 4.0
- Smart Thermocouples:
- Equipped with integrated electronics for self-diagnosis and communication.
- Provide real-time data to central control systems, enabling predictive maintenance and process optimization.
- Wireless Thermocouples:
- Eliminate the need for extensive cabling in large steel plants.
- Facilitate easier installation and maintenance, and enhance flexibility in monitoring hard-to-reach areas.
- Internet of Things (IoT):
- Thermocouples connected to IoT platforms allow for remote monitoring and control.
- Data from multiple thermocouples can be aggregated and analyzed for comprehensive process insights.
Advanced Process Control
- Closed-Loop Control Systems:
- Thermocouples integrated into closed-loop control systems provide real-time feedback.
- Enable automatic adjustments to maintain optimal temperature conditions, improving process stability and product quality.
- Machine Learning and AI:
- Data from thermocouples is used to train machine learning models that predict process outcomes and identify anomalies.
- AI algorithms optimize temperature control strategies, enhancing efficiency and reducing energy consumption.
Case Studies and Success Stories
- Bhilai Steel Plant:
- One of India’s largest and most prominent steel plants, Bhilai has implemented advanced thermocouple systems.
- Enhanced temperature monitoring has led to significant improvements in product quality and process efficiency.
- Raipur Steel Units:
- Smaller steel production units in Raipur have adopted wireless thermocouples for ease of installation and maintenance.
- This has reduced downtime and maintenance costs while ensuring consistent temperature monitoring.
- Durg Steel Industries:
- Durg-based steel manufacturers have integrated smart thermocouples into their automation systems.
- Real-time data and predictive analytics have improved operational decision-making and reduced production risks.
Future Trends and Developments
- Nanotechnology:
- Research is underway to develop thermocouples using nanomaterials, offering enhanced sensitivity and durability.
- These next-generation sensors could provide even more accurate and reliable temperature measurements.
- Advanced Materials:
- Development of new alloys and ceramics for thermocouple construction to withstand even harsher environments.
- Improved materials will enhance the lifespan and performance of thermocouples in steel plants.
- Integrated Sensor Networks:
- Future steel plants may deploy extensive networks of interconnected thermocouples for comprehensive thermal mapping.
- Such networks will provide detailed insights into temperature distributions, enabling precise control and optimization.
Thermocouples are indispensable in Chhattisgarh’s steel plants, contributing to efficient and safe steel production. Continuous advancements in thermocouple technology and integration with automation systems promise to further enhance the performance and reliability of temperature measurement in these critical industrial environments.