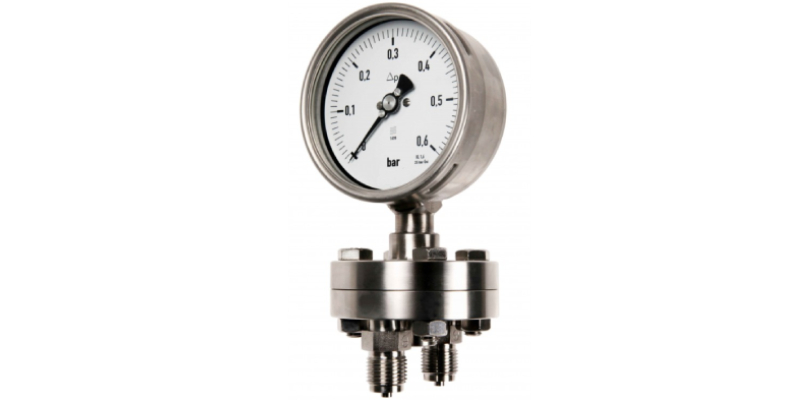
A differential pressure gauge is a device used to measure the difference in pressure between two points in a fluid system. These gauges are essential in various industries, including HVAC, automotive, manufacturing, and process control.
Types of Differential Pressure Gauges:
- Bourdon Tube Differential Pressure Gauge:
- This type of gauge uses a curved tube made of materials like brass or stainless steel.
- When there is a pressure difference between the two ports, the tube tends to straighten or curve, which is translated into a pressure reading on a dial.
- It’s a mechanical gauge and is widely used due to its simplicity and reliability.
- Diaphragm Differential Pressure Gauge:
- Diaphragm gauges use a flexible diaphragm made of materials like metal or elastomers.
- When pressure differential occurs, the diaphragm flexes and this movement is linked to a pointer, providing a pressure reading.
- They are suitable for low-pressure applications and are often used in industries like pharmaceuticals and food processing.
- Digital Differential Pressure Gauge:
- Digital gauges use electronic sensors to measure pressure differences and display the results digitally.
- They are precise, easy to read, and offer various advanced features like data logging and alarm settings.
- Digital gauges are commonly used in laboratories, research facilities, and industrial automation.
- Piston Differential Pressure Gauge:
- These gauges employ a piston or piston-cylinder arrangement.
- Pressure difference causes the piston to move, and this displacement is correlated with pressure readings.
- They are known for their accuracy and are often used in critical applications.
Advantages of Differential Pressure Gauges:
- Measurement of Pressure Difference: The primary advantage of these gauges is their ability to measure the pressure difference between two points in a system accurately. This is vital for various industrial processes and HVAC systems to ensure proper operation.
- Wide Range of Applications: Differential pressure gauges find applications in a diverse range of industries, including HVAC, petrochemical, pharmaceutical, and manufacturing, making them versatile instruments.
- Reliability: Mechanical differential pressure gauges, such as Bourdon tube gauges, are known for their durability and reliability. They can withstand harsh operating conditions and require minimal maintenance.
- Precision: Digital differential pressure gauges provide high precision and accuracy in pressure measurement. They are often preferred for critical applications where precise control is essential.
- Real-time Monitoring: Digital gauges offer real-time monitoring and data recording capabilities, allowing operators to track pressure differentials over time and make informed decisions.
- Alarm and Control Features: Some digital differential pressure gauges come equipped with alarm settings, which can trigger alerts when pressure reaches predefined thresholds, enhancing safety and efficiency.
- Remote Monitoring: Digital gauges can be integrated into control systems, allowing for remote monitoring and control of pressure differentials, which is especially useful in industrial automation.
In conclusion, differential pressure gauges come in various types, each suited to specific applications and requirements. Their advantages include accurate pressure differential measurement, reliability, and versatility, making them indispensable tools in numerous industries. The choice of the right gauge depends on factors such as the application, pressure range, and environmental conditions.