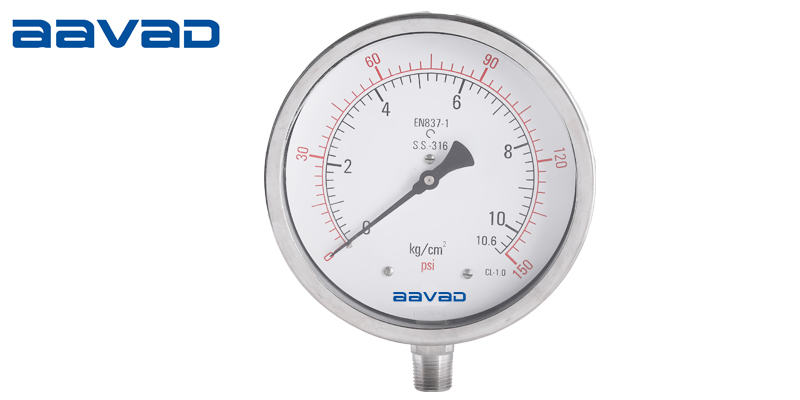
AAVAD Industrial pressure gauges are essential instruments used to measure and monitor the pressure in various industrial applications. They provide crucial information about fluid or gas pressures, ensuring the safe and efficient operation of systems and equipment. When choosing a pressure gauge for your business, it’s important to consider several factors to ensure you select the right option. Here’s a guide to help you make an informed decision:
Pressure Range: Determine the pressure range you need to measure. Pressure gauges are available in different ranges, such as low, medium, and high pressure. Ensure the gauge you choose can accurately measure the pressure within your desired range.
Pressure Type: Consider the type of pressure you need to measure. Pressure gauges can measure different types, including gauge pressure (relative to atmospheric pressure), absolute pressure, differential pressure, and vacuum pressure. Select a gauge that suits your specific pressure measurement requirements.
Accuracy: Assess the level of accuracy you require. Pressure gauges have different accuracy levels, typically expressed as a percentage of the full-scale reading. Higher accuracy gauges are generally more expensive but provide more precise measurements. Determine the acceptable level of accuracy for your application.
Gauge Size: Consider the size of the pressure gauge, including the diameter of the dial face. Choose a size that allows for easy reading of the pressure values from a reasonable distance. Ensure it fits into the available space in your system or equipment.
Mounting Options: Determine how you plan to mount the pressure gauge. Common mounting options include panel mount, surface mount, and direct mount. Select a gauge with a suitable mounting style that integrates well with your equipment or system.
Environmental Conditions: Evaluate the environmental conditions in which the pressure gauge will operate. Factors like temperature, pressure fluctuations, vibration, and corrosive or hazardous substances can affect gauge performance. Ensure the gauge is designed to withstand the specific conditions of your application.
Material Compatibility: Consider the material compatibility requirements. Pressure gauges are available in various materials, such as brass, stainless steel, or plastic. Ensure the gauge’s wetted parts (those in contact with the process fluid) are compatible with the substance being measured to prevent corrosion or contamination.
Display Type: Decide on the type of display that suits your needs. Pressure gauges can have analog dials, digital displays, or a combination of both. Analog dials are traditional and widely used, while digital displays provide precise readings and additional features. Choose the display type that offers clear visibility and ease of reading.
Additional Features: Determine if you require any additional features, such as limit switches, data logging capabilities, or remote monitoring options. These features can enhance the functionality and convenience of the pressure gauge, depending on your specific application.
Budget: Finally, consider your budget constraints. Pressure gauges vary in price based on their features, accuracy, and durability. Set a budget and choose a gauge that strikes the right balance between cost and performance.
Gauge Type: There are various types of pressure gauges available, such as bourdon tube gauges, diaphragm gauges, capsule gauges, and differential pressure gauges. Each type has its own advantages and limitations. Research and select the type that best fits your application requirements.
Calibration: Determine if the pressure gauge requires periodic calibration. Regular calibration ensures the gauge maintains accuracy over time. Some gauges can be calibrated on-site, while others may need to be sent to a calibration facility. Consider the calibration process and frequency to maintain accurate measurements.
Pressure Unit: Verify that the pressure unit of the gauge matches the unit of measurement used in your industry or application. Common units include psi (pounds per square inch), bar, kPa (kilopascal), or MPa (megapascal). Ensure the pressure gauge displays the appropriate unit for easy interpretation of readings.
Shock and Vibration Resistance: If your application involves high levels of vibration or shock, consider a pressure gauge specifically designed to withstand these conditions. Such gauges have additional features, like dampening mechanisms or rugged construction, to prevent damage and maintain accurate readings.
Certification and Compliance: Determine if your industry or application requires specific certifications or compliance with standards. Examples include ISO, ANSI, or ASME certifications. Ensure the pressure gauge meets the necessary requirements to ensure safety, reliability, and regulatory compliance.
Maintenance and Serviceability: Consider the ease of maintenance and serviceability of the pressure gauge. Some gauges require regular cleaning, lubrication, or part replacements. Ensure that the gauge can be easily accessed and serviced to minimize downtime and maintenance costs.
Supplier Reputation and Support: Research the reputation and reliability of the pressure gauge supplier. Look for manufacturers or distributors known for producing high-quality instruments and providing excellent customer support. A reputable supplier can offer technical assistance, warranty coverage, and prompt replacement or repair services if needed.
Future Expansion and Compatibility: If you anticipate future changes or expansions in your system, consider the compatibility of the pressure gauge with potential modifications. Ensure the gauge allows for easy integration, upgrades, or additional functionalities to adapt to your evolving needs.
Industry-specific Requirements: Certain industries may have unique requirements for pressure gauges. For example, in the food or pharmaceutical industries, gauges with sanitary connections and hygienic design may be necessary. Understand the specific demands of your industry and choose a gauge that meets those requirements.
User Training and Familiarity: Assess the ease of use and familiarity of the pressure gauge for your operators and maintenance personnel. Opt for gauges that are user-friendly and require minimal training for proper operation. Clear labeling and intuitive design can contribute to efficient and error-free readings.
By considering these additional factors along with the ones mentioned earlier, you can make a well-informed decision when selecting the most suitable industrial pressure gauge for your business.