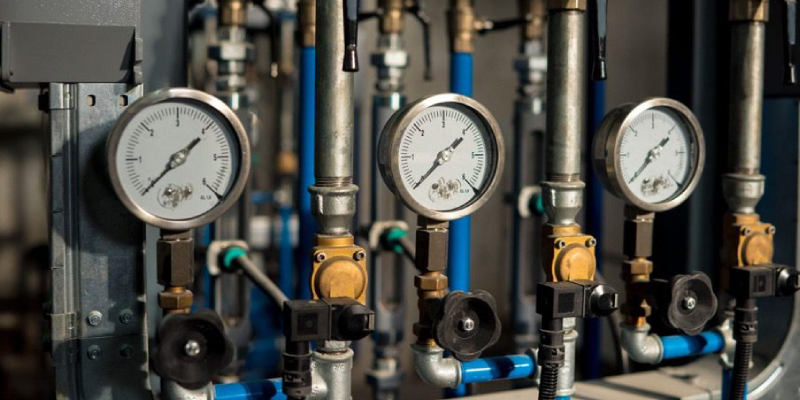
Introduction: In industrial settings, safety is of paramount importance. Monitoring critical parameters like pressure and temperature is essential to prevent equipment failures, process malfunctions, and potential hazards. Pressure gauges and temperature gauges are two crucial instruments that provide real-time information about the conditions within a system. In this blog, we’ll delve into the significance of pressure and temperature gauges, their functioning, and their roles in maintaining safety.
Pressure Gauges: Pressure gauges are devices used to measure the pressure of gases or liquids within a closed system. They are found in a wide range of applications, from industrial machinery to HVAC systems. The primary purpose of a pressure gauge is to provide operators with an accurate and real-time reading of the pressure, helping them ensure that a system operates within safe limits.
Functioning of Pressure Gauges: Pressure gauges typically consist of a Bourdon tube, which is a curved, hollow metal tube that expands or contracts with changes in pressure. As the pressure within the system increases, the Bourdon tube straightens out, and this movement is transferred to a mechanical linkage, causing the gauge’s needle to move across the pressure scale, indicating the pressure reading.
Importance in Safety: Pressure gauges play a vital role in maintaining safety in various scenarios:
- Pressure Limit Monitoring: Pressure gauges help operators monitor if the pressure within a system is exceeding safe limits. This prevents potential equipment failures, leaks, and explosions.
- Leak Detection: A sudden drop in pressure might indicate a leak in the system. Detecting leaks early can prevent environmental contamination and hazardous situations.
- Process Control: Pressure gauges aid in optimizing processes by ensuring that pressure-sensitive operations are carried out under optimal conditions.
Temperature Gauges: Temperature gauges, as the name suggests, measure the temperature of a medium, such as a fluid or a gas. These gauges are essential for processes that involve heat transfer, such as chemical reactions, power generation, and refrigeration.
Functioning of Temperature Gauges: There are various types of temperature gauges, including bimetallic, gas-filled, and digital thermometers. Bimetallic thermometers use the expansion of two different metals to indicate temperature changes, while gas-filled thermometers use the expansion of a gas to achieve the same effect. Digital thermometers, on the other hand, use electronic sensors to provide precise temperature readings.
Importance in Safety: Temperature gauges contribute to safety in the following ways:
- Overheating Prevention: In industrial processes, overheating can lead to equipment damage or even fires. Temperature gauges warn operators if temperatures exceed safe thresholds.
- Cooling System Monitoring: Temperature gauges are crucial in systems that require cooling, such as engines and industrial equipment. They ensure that cooling systems are functioning properly.
- Process Optimization: Temperature control is often critical in chemical reactions and manufacturing processes. Temperature gauges help maintain consistency and product quality.
Pressure Gauges:
Types of Pressure Gauges:
- Bourdon Tube Gauges: As mentioned earlier, these are the most common type of pressure gauges. They are suitable for a wide range of applications, from low to high pressures. Bourdon tubes can be made from different materials such as brass, bronze, stainless steel, or even plastics, depending on the medium being measured.
- Diaphragm Gauges: These gauges use a flexible diaphragm that deforms with changes in pressure. They are ideal for measuring low-pressure ranges and are often used in applications where the medium might clog or corrode traditional Bourdon tubes.
- Bellows Gauges: Bellows gauges use a collapsible bellows element to measure pressure changes. They are sensitive and suitable for low-pressure measurements, vacuum applications, and where precise pressure readings are required.
- Manometers: Manometers are a type of pressure gauge that use a column of liquid to measure pressure. U-tube manometers, well-type manometers, and inclined-tube manometers are some common types.
Applications of Pressure Gauges:
- Industrial Processes: Pressure gauges are essential in various industries such as chemical, petrochemical, oil and gas, and manufacturing. They monitor processes like steam generation, fluid circulation, and hydraulic systems.
- HVAC Systems: Pressure gauges are used to monitor air pressure in heating, ventilation, and air conditioning systems to ensure optimal airflow and system efficiency.
- Automotive: Pressure gauges are found in vehicle engines to monitor oil pressure, fuel pressure, and tire pressure, ensuring safe and efficient operation.
- Medical Equipment: Pressure gauges are used in medical devices like blood pressure monitors and ventilators to provide accurate readings for patient care.
Temperature Gauges:
Types of Temperature Gauges:
- Bimetallic Thermometers: These consist of two different metals bonded together. As temperature changes, the metals expand or contract at different rates, causing the bimetallic strip to bend, which is then translated into a temperature reading.
- Gas-Filled Thermometers: These gauges use a gas-filled bulb connected to a capillary tube. As the gas expands or contracts with temperature changes, it moves the liquid inside the tube, which is then used to indicate the temperature.
- Digital Thermometers: These modern gauges use electronic sensors like thermocouples or resistance temperature detectors (RTDs) to measure temperature. The readings are displayed digitally, providing high accuracy and quick response.
Applications of Temperature Gauges:
- Chemical Processing: Temperature control is critical in chemical reactions to ensure product quality and safety. Temperature gauges monitor and regulate heat-intensive processes.
- Power Generation: Power plants use temperature gauges to monitor the temperature of cooling systems, turbines, and boilers to prevent overheating and equipment damage.
- Food and Beverage Industry: Temperature gauges are essential for maintaining proper food storage and processing temperatures, ensuring food safety and quality.
- Laboratories: Scientific research often requires precise temperature control. Temperature gauges play a role in maintaining controlled environments for experiments.
- Environmental Monitoring: Temperature gauges are used to monitor environmental conditions in weather stations, climate studies, and ecology research.
Conclusion: Pressure gauges and temperature gauges are indispensable tools in ensuring safety and efficiency in various industrial processes. By providing real-time measurements of pressure and temperature, these instruments empower operators to make informed decisions, prevent disasters, and optimize processes. Whether it’s preventing equipment failures due to high pressure or maintaining controlled temperatures for chemical reactions, pressure gauges and temperature gauges are the silent guardians of industrial safety.