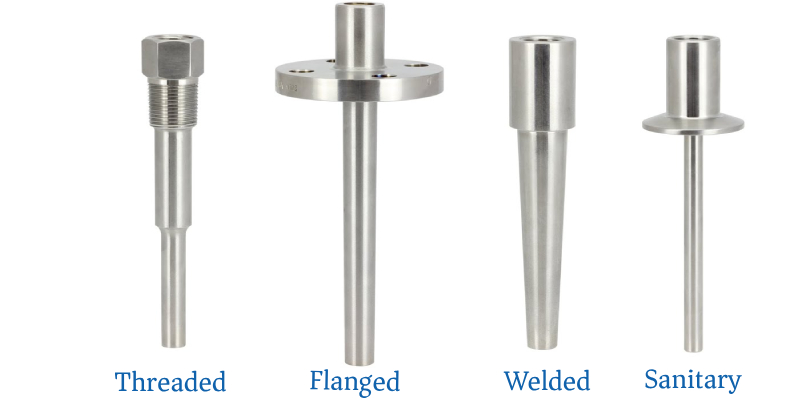
A thermowell is a cylindrical fitting used in industrial processes to protect temperature sensors, such as thermocouples or resistance temperature detectors (RTDs), from harsh environmental conditions. It is typically made of metal or other durable materials and is designed to encase and shield the temperature sensor while allowing it to accurately measure the temperature of a fluid or gas.
Here’s why thermowell are required and their significance in various industrial applications:
Protection: Thermowells protect temperature sensors from corrosive, abrasive, or otherwise harsh process media. This is important because many temperature sensors are sensitive and can be easily damaged by exposure to the process fluid. A thermowell acts as a barrier, preventing direct contact between the sensor and the fluid.
Maintenance: When a temperature sensor needs to be replaced or serviced, it can be done easily without interrupting the process or draining the system. Without a thermowell, removing or replacing a sensor would require shutting down the system, which can be costly and time-consuming.
Pressure Resistance: In high-pressure applications, thermowells are essential for maintaining the integrity of the temperature sensor. The thermowell can withstand the pressure of the process, ensuring the sensor remains safe and operational.
Flow Dynamics: The design of a thermowell is critical in maintaining the flow dynamics of the fluid or gas being measured. It should minimize the impact on the flow to ensure accurate temperature readings.
Compatibility: Thermowells can be made from various materials to suit the specific requirements of the process fluid. Different materials offer different levels of corrosion resistance, temperature resistance, and compatibility with different fluids.
Versatility: Thermowells are used in a wide range of industries, including chemical processing, oil and gas, food and beverage, pharmaceuticals, and more. They are versatile and adaptable to different applications.
Temperature Range: Thermowells are designed to accommodate a wide range of temperature measurements, from extremely low cryogenic temperatures to extremely high temperatures found in processes like metallurgy and combustion. The choice of material for the thermowell is crucial in ensuring it can withstand these temperature extremes.
Chemical Compatibility: In industries where corrosive or reactive fluids are present, the selection of the thermowell material becomes critical. Different materials such as stainless steel, Inconel, Hastelloy, or ceramic can be chosen based on the chemical compatibility with the process fluid. This prevents the sensor from being corroded or damaged.
Vibration and Mechanical Protection: In applications with high levels of vibration or mechanical stress, thermowells act as shock absorbers, protecting the temperature sensor from mechanical damage. This is common in industries like aerospace, automotive, and heavy machinery manufacturing.
Hygienic Environments: In the food and pharmaceutical industries, where strict hygiene standards must be maintained, thermowells are often used with specialized designs that allow for easy cleaning and prevent the accumulation of contaminants.
Response Time: The design of a thermowell can influence the response time of the temperature sensor. A well-designed thermowell minimizes the lag in temperature measurement, ensuring that changes in the process are accurately and promptly detected.
Different Types: Thermowells come in various shapes and configurations, including straight, tapered, stepped, and flanged designs. The choice of thermowell type depends on factors like process conditions, space constraints, and installation requirements.
Compliance with Standards: In many industries, there are strict regulations and standards governing temperature measurement. Thermowells are often designed and manufactured to comply with these standards, ensuring accurate and reliable temperature readings for compliance and safety purposes.
Customization: In some cases, custom-designed thermowells are necessary to meet specific process requirements. Manufacturers can create thermowells tailored to the unique needs of a particular application.
Thermal Isolation: In processes where the temperature sensor needs to be isolated from the surrounding environment, thermowells with insulating properties can be used. These prevent heat transfer to or from the sensor, ensuring accurate temperature measurements.
In conclusion, thermowells play a crucial role in ensuring the accuracy, safety, and longevity of temperature measurement in a wide range of industrial settings. Their design, material selection, and configuration are highly dependent on the unique characteristics and demands of each application, making them a versatile and indispensable component in process control and monitoring systems.